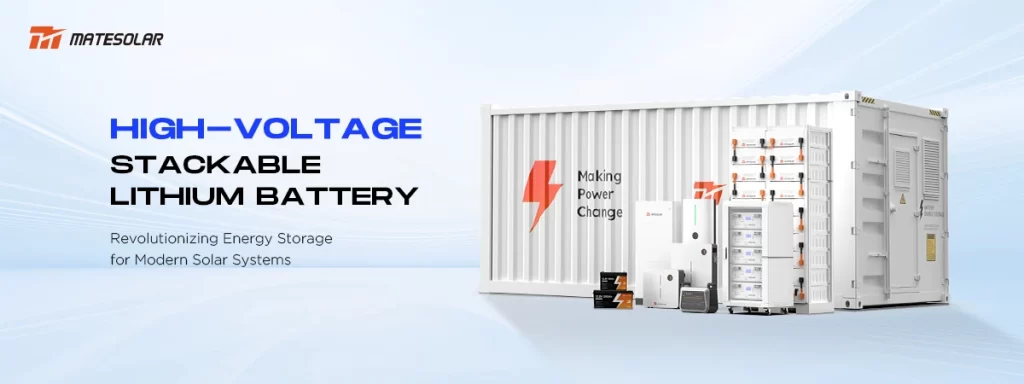
Modular design, high energy density, and safety innovations redefine industrial and commercial energy management.
The Architectural Shift: Why Stackable High-Voltage Systems?
Traditional flat-array battery systems face spatial constraints and scalability challenges. In response, vertical high-voltage stackable lithium batteries have emerged—built by vertically stacking and serially connecting battery modules into high-voltage systems. This design achieves up to 40% higher space utilization compared to conventional setups while enabling flexible capacity expansion from 10kWh to over 1MWh through modular stacking.
Core advantages include:
1. Reduced cabling complexity: High-voltage architecture (192V–1000V) minimizes current resistance and power loss;
2. Thermal management optimization: Vertical stacking facilitates uniform air/liquid cooling, critical for safety;
3. AI-driven controllability: Embedded BMS with multi-level protection (cell/rack/system) enables granular monitoring.
Technical Innovations Driving Performance
1. Next-Gen Cell Manufacturing
The shift from winding to stacking processes is pivotal. For example, Honeycomb Energy’s 3rd-gen "Flying Stack" (0.125s per stack) eliminates the risk of metal deposition unevenness—common in wound cells’ curved corners. This boosts cycle life to 6,000+ cycles and supports 6C ultra-fast charging for EVs and grid buffers.
2. Safety Redefined
<1> Dual-fire suppression: Cabinet-level fluoroketone + pack-level aerosol fire protection (GoodWe’s 261kWh cabinet);
<2> Thermo-electric separation: Honeycomb’s "Dragon Scale" battery isolates thermal runaway channels from electrical paths;
<3> Structural armor: 1000J impact resistance (6× national standards).
3. Grid Intelligence Integration
GoodWe’s Jiangxi project exemplifies "source-grid-load-storage-intelligence" integration:
<1> 630kWp solar + 1827kWh storage powers 26 heavy-duty EV chargers (320kW each);
<2> Zero grid backflow: AI curtails solar generation when storage is full;
<3> Price arbitrage: Storage charges during off-peak hours to offset peak tariffs.
Table: Comparative Analysis of Energy Storage Solutions
Parámetro | Traditional Li-ion | Stackable HV LiFePO₄ | Mejora |
Energy Density (Wh/L) | 200–250 | 350–500 | +75%–100% |
Cycle Life (cycles) | 3,000–4,000 | ≥6,000 | +50%–100% |
Deployment Flexibility | Fixed capacity | Modular (5kWh/unit) | Near-unlimited |
Installation Time | Weeks | <72 hours | –70% |
Safety Certification | UL1973 | UL9540A + UN38.3 | Enhanced |
Real-World Deployments: From Data Centers to Heavy Trucking
1. Heavy-Duty Transport Electrification
GoodWe’s De’an project (China’s first renewable-powered heavy-truck charging station) combines:
<1> 630.63kWp solar + 30kW wind + 1,827kWh storage;
<2> Dynamic grid compliance: Prevents reverse flow during overproduction;
<3> 261kWh outdoor-rated cabinets (IP55) with liquid cooling.
2. Ultra-Fast Charging Networks
Honeycomb’s 4C "Dragon Scale" battery achieves:
<1> 20%→80% SOC in 12.1 minutes;
<2> 800km range (PHEV) with 65kWh capacity;
<3> Compatibility with 800V charging infrastructure.
Market Growth and Projections
Though currently a niche segment (0.5% of China’s LiFePO₄ market in 2024, ~3.57B RMB), stackable HV systems are projected to grow at 85% CAGR through 2028. Key drivers include:
<1> Demand from data centers requiring 99.999% uptime;
<2> "PV red zones" restricting grid feed-in (e.g., China’s post-531 policy);
<3> Falling system costs: $650/kWh at 100-unit scale.
Table: Market Outlook for Stackable HV Batteries (2023–2027)
Segmento | 2023 Size (GWh) | 2024 Size (GWh) | 2027F (GWh) | Primary Applications |
Industrial & Commercial | 0.48 | 0.51 | 3.2 | Peak shaving, backup power |
EV Charging Hubs | 0.05 | 0.12 | 1.1 | Buffering for ultra-fast EV charging |
Microgrids | 0.03 | 0.08 | 0.9 | Island-mode renewable stabilization |
Data Centers | 0.02 | 0.04 | 0.5 | UPS replacement |
Q&A: Addressing Key Industry Queries
Q1: How do stackable systems handle cell balancing at high voltages?
A: Multi-tiered BMS architecture balances cells individually (via BMUs) while synchronizing racks via CAN bus. Active balancing currents up to 5A prevent drift during 150+ module stacks.
Q2: What fire safety certifications exist?
A: Leading systems comply with IEC 62619 (safety) and UL 9540A (fire propagation). GoodWe’s cabinets integrate dual-agent suppression (fluoroketone + aerosol), exceeding NFPA 855 standards.
Q3: Can older storage systems integrate with new HV stacks?
A: Not directly—voltage matching requires DC-DC converters. However, hybrid AC-coupling solutions exist (e.g., using SEC3000 controllers).
El camino a seguir
Vertical high-voltage stackable batteries are transitioning from niche solutions to mainstream infrastructure. With Honeycomb targeting 220Wh/kg high-manganese iron-nickel cells and GoodWe advancing virtual power plant (VPP) integration, this technology will underpin tomorrow’s resilient, software-defined grids.
For solar developers, this means:
<1> Reduced LCOE via 30+ year system lifetimes;
<2> Scalability from 10kWh (SMEs) to multi-MWh (industrial parks);
<3> New revenue streams via VPP participation and frequency regulation.
MateSolar delivers integrated PV-storage solutions leveraging stackable HV technology—empowering enterprises to harness sunlight, store it intelligently, and deploy it precisely. Because energy transition isn’t about generating more. It’s about managing it better.